[ad_1]
Revolutionizing Manufacturing with Digital Twins: From Concept to Reality
In the manufacturing industry, staying competitive and efficient has always been a top priority. With the rapid advancement of technology, a new concept called digital twins has emerged, promising to revolutionize the entire manufacturing process from start to finish. Digital twins are virtual representations of physical objects or systems, and they have the potential to transform the traditional approach to manufacturing into a more streamlined and cost-effective one.
The concept of digital twins may seem futuristic, but it is rapidly becoming a reality in various industries. From simple objects like individual machine components to complex systems such as entire production lines or even entire factories, digital twins can provide a virtual mirror image that enables advanced analysis and simulation.
One of the key benefits of digital twins is the ability to monitor and analyze real-time data. By connecting physical objects to their virtual counterparts, manufacturers can collect and analyze data on performance, wear and tear, and overall efficiency. This data can then be used to identify areas for improvement, optimize processes, and reduce maintenance costs. For example, if a manufacturing plant has a digital twin of its production line, it can monitor variables such as speed, energy consumption, and error rates to identify bottlenecks and optimize operations.
Digital twins also enable predictive maintenance, which can significantly reduce downtime and costs. By continuously monitoring the performance of physical objects and comparing it to their virtual counterparts, manufacturers can detect potential failures or malfunctions before they occur. This allows for proactive maintenance, preventing costly breakdowns and ensuring optimal performance.
Moreover, digital twins enable virtual testing and simulation. Before a physical object is even produced, a virtual replica can be created and tested under various conditions. This allows manufacturers to identify potential issues and optimize designs before investing in expensive physical prototypes. It also enables quick adjustments and modifications as needed, saving time and resources.
Another advantage of digital twins is the ability to optimize production in real-time. By connecting virtual models to actual production processes, manufacturers can continuously assess and adapt their operations based on real-time data. This flexibility allows for better demand forecasting, less waste, and improved agility in responding to market changes.
The potential applications of digital twins in manufacturing are vast. They can be used to optimize workflows, improve quality control, enhance supply chain management, and even enable remote troubleshooting and support. As the technology continues to advance, the possibilities will only grow.
However, adopting digital twins is not without challenges. It requires investment in technology infrastructure, data analytics capabilities, and workforce training. Additionally, manufacturers need to ensure data security and privacy, as well as find ways to integrate digital twins into existing systems and processes.
In conclusion, digital twin technology is revolutionizing manufacturing by providing virtual models that enable advanced analysis, simulation, and optimization. With real-time data monitoring, predictive maintenance, virtual testing, and agile production optimization, manufacturers can achieve increased efficiency, reduce costs, and stay competitive in a rapidly changing market. While implementing digital twins may present some challenges, the benefits they offer make it an investment worth considering for any manufacturing company seeking to embrace Industry 4.0 and beyond.
[ad_2]
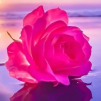